Dynamic characteristics of turbomachinery
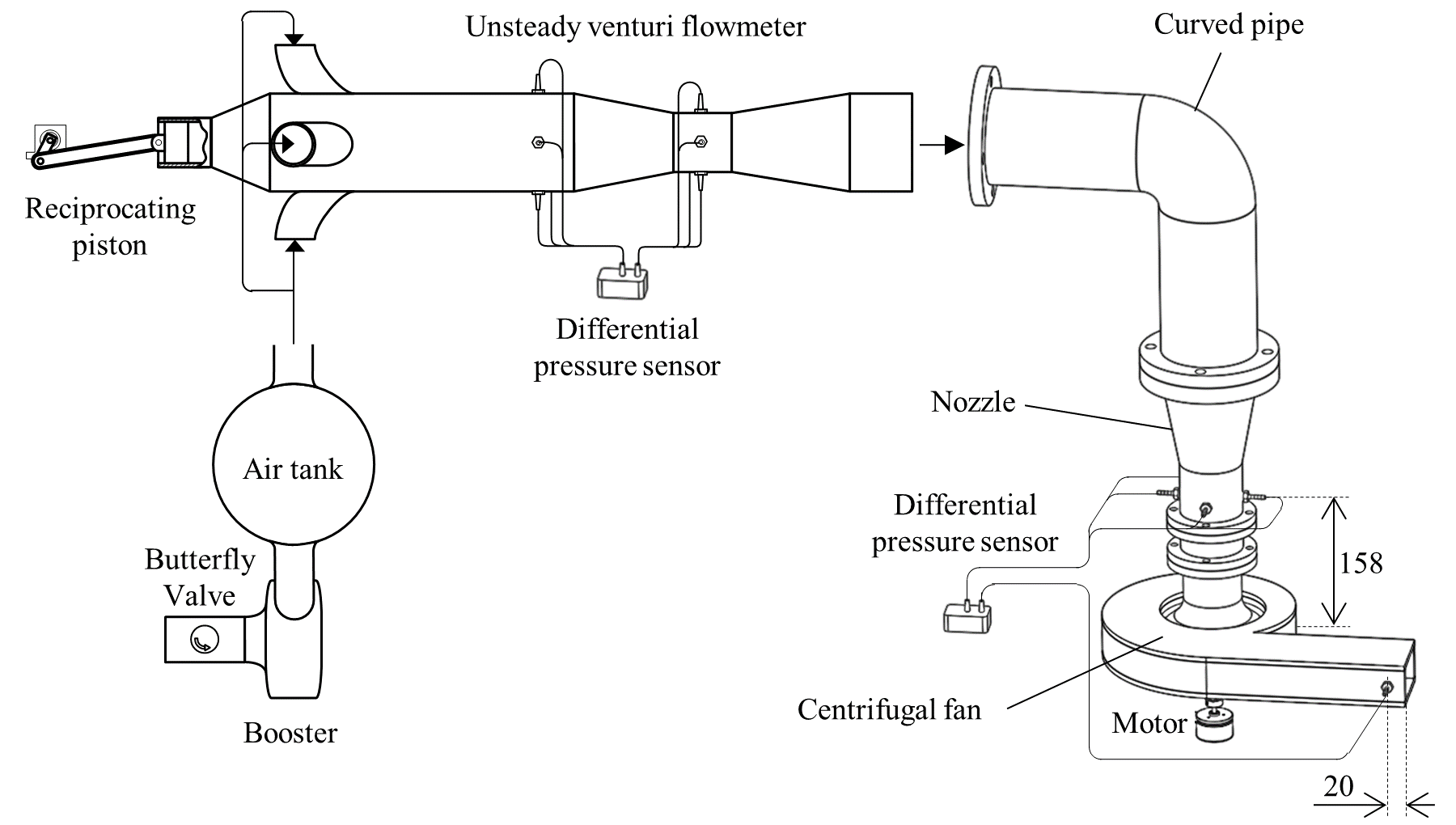
Estimation for dynamic characteristics of cavitating pump
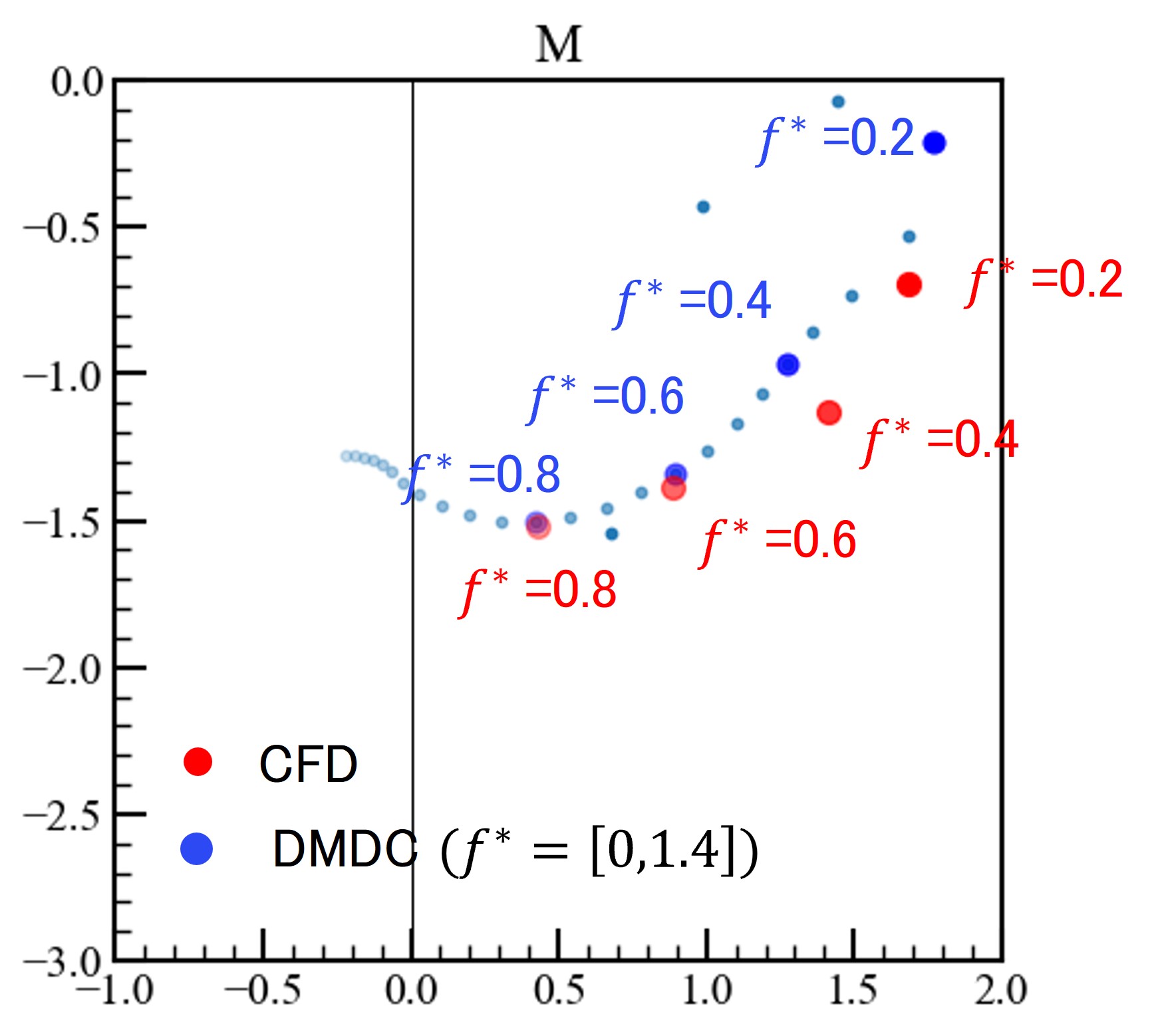
Digital twin of turbomachinery
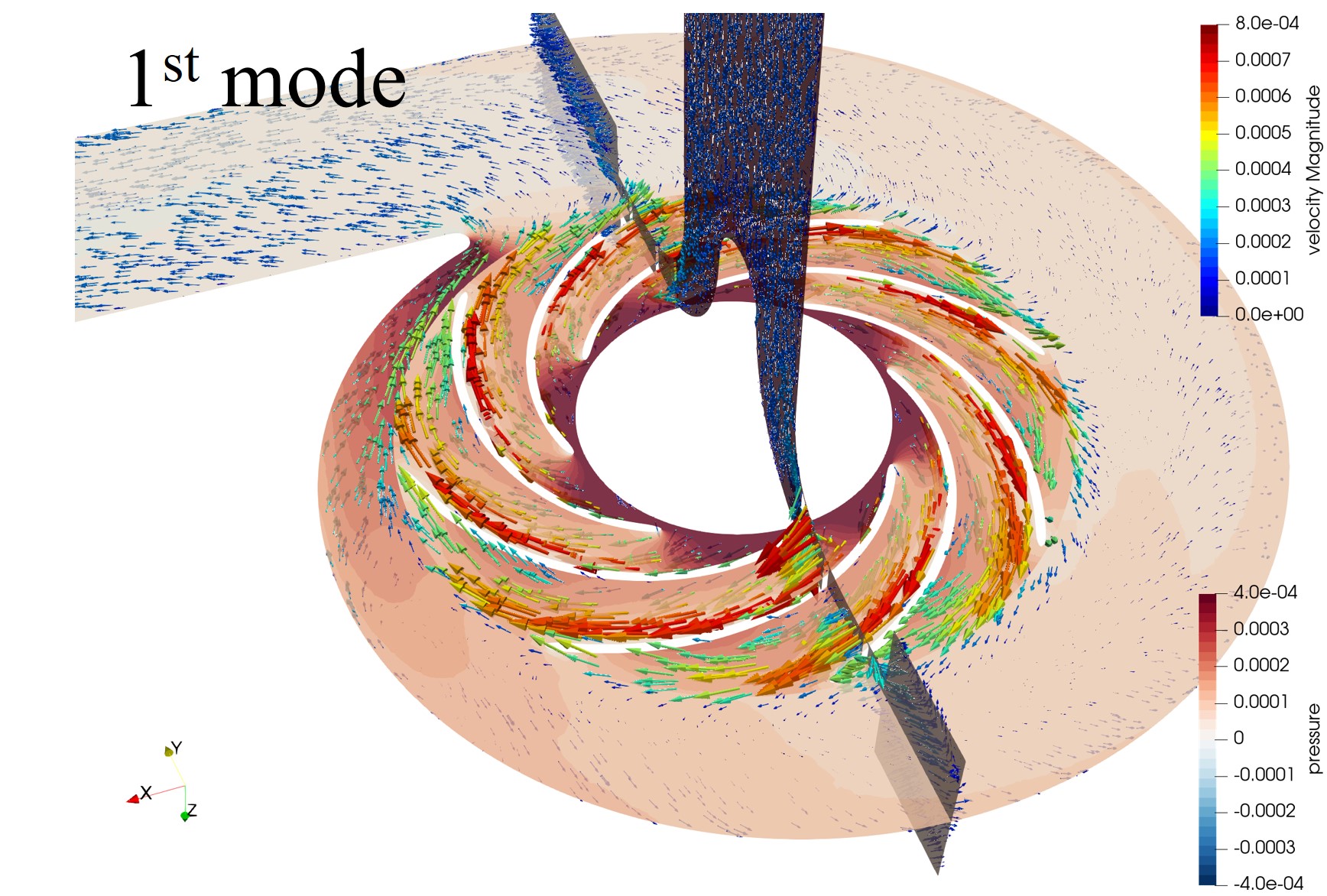
Inverse design for Turbomachinery
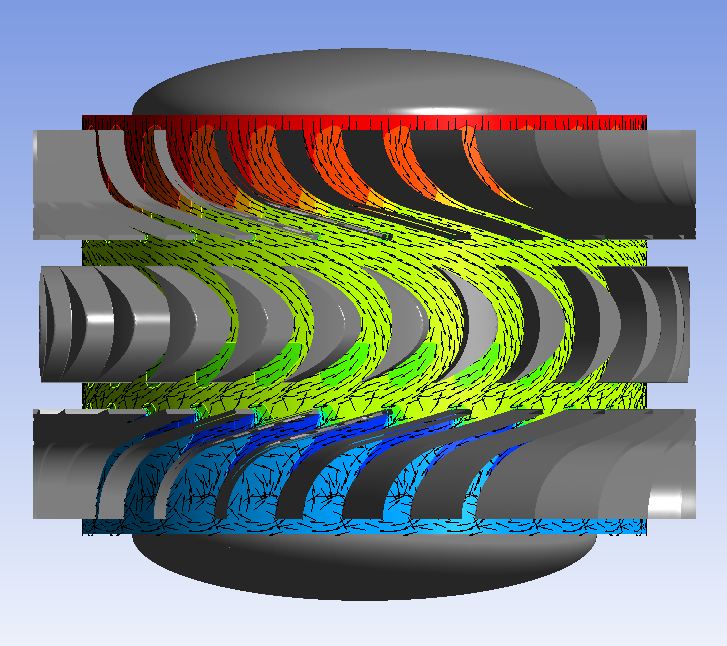
Unsteady flow around impeller with forward curved vanes
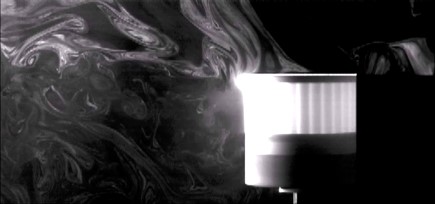
Water Entry Dynamics
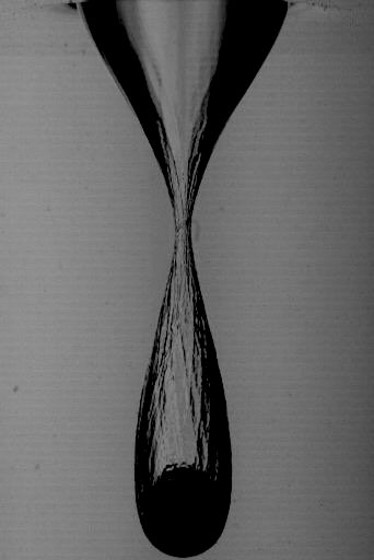
Water Drop Explosion in the Hot Cooking Oil
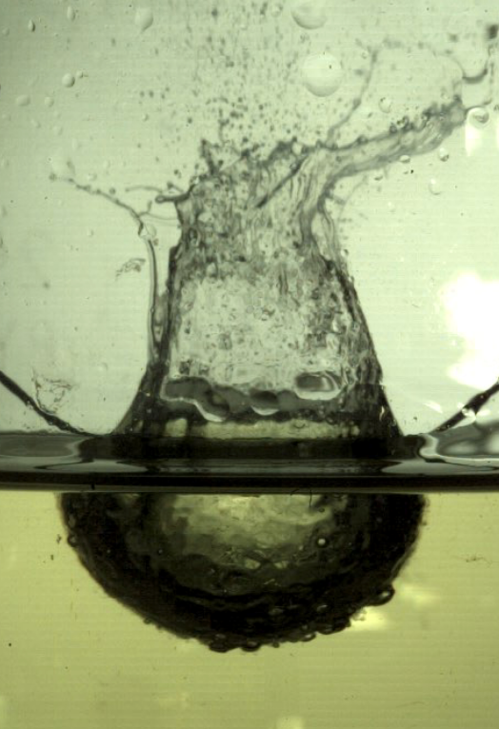
Active control of cavitation surge in hydraulic system
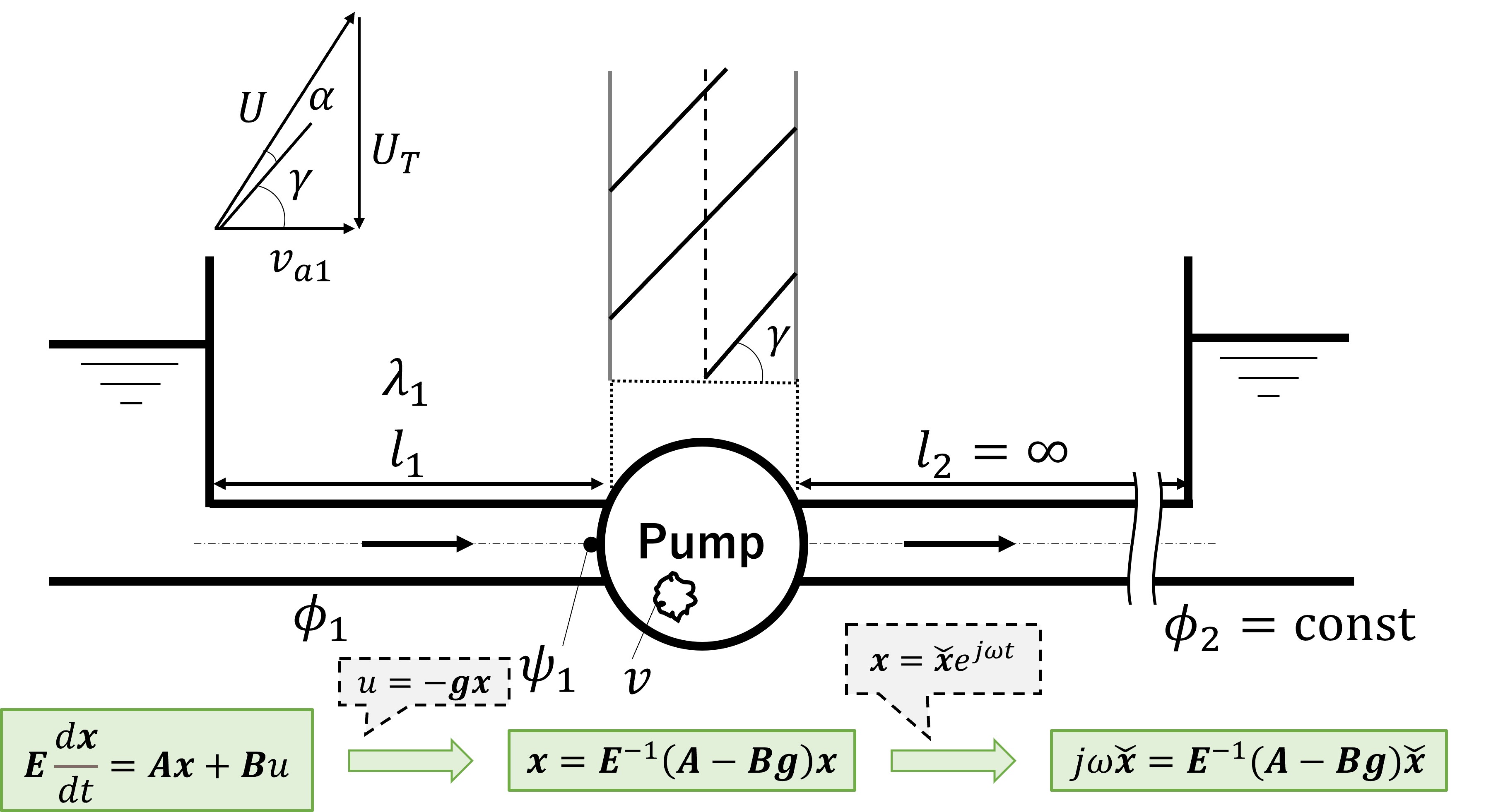
Active control of flow separation
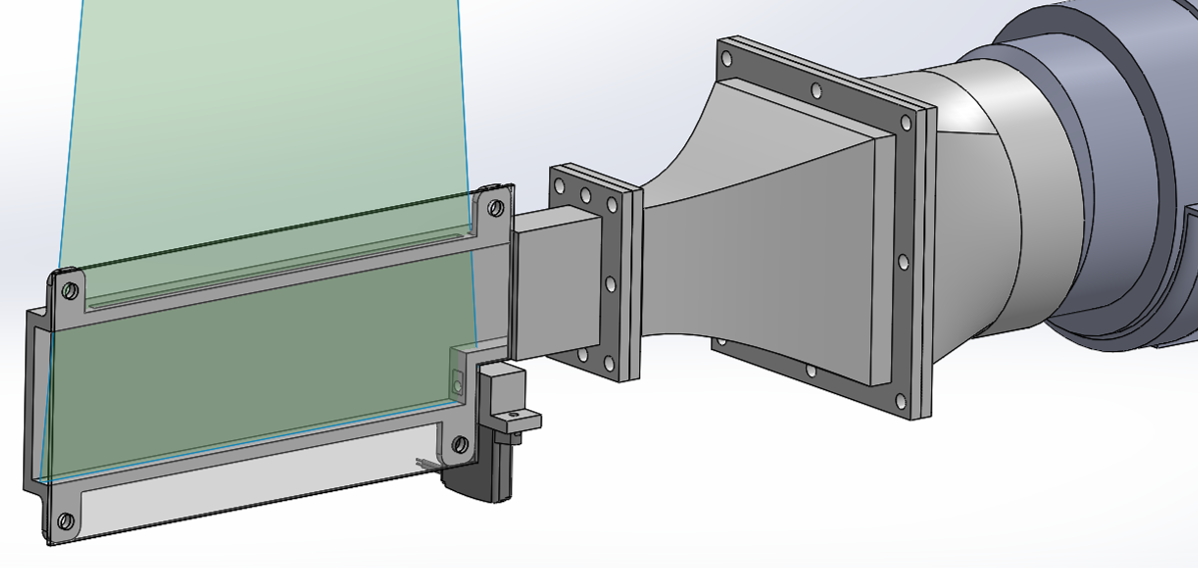
Construction of a digital twin for hydrogen generation reactor
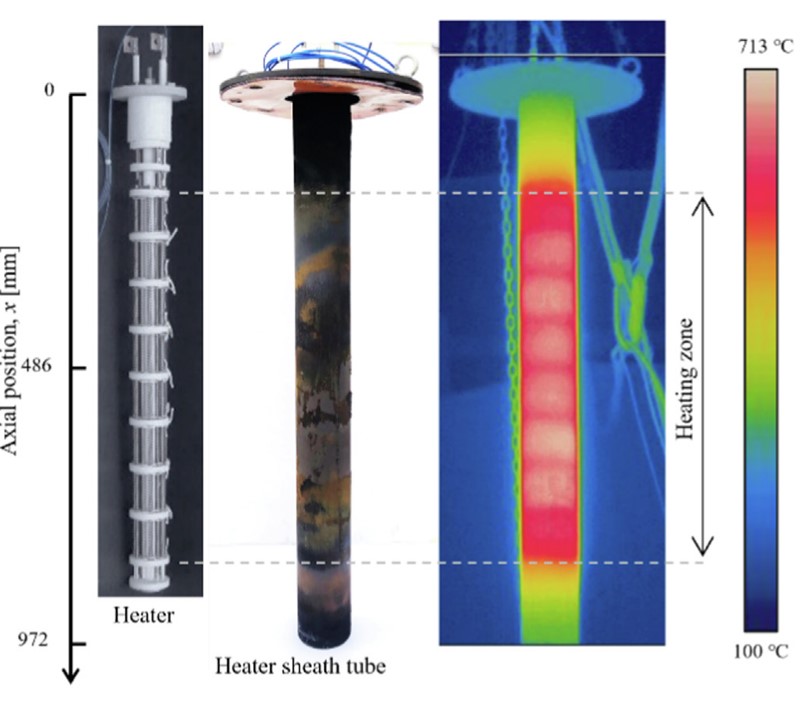
Laser-induced Cavitation
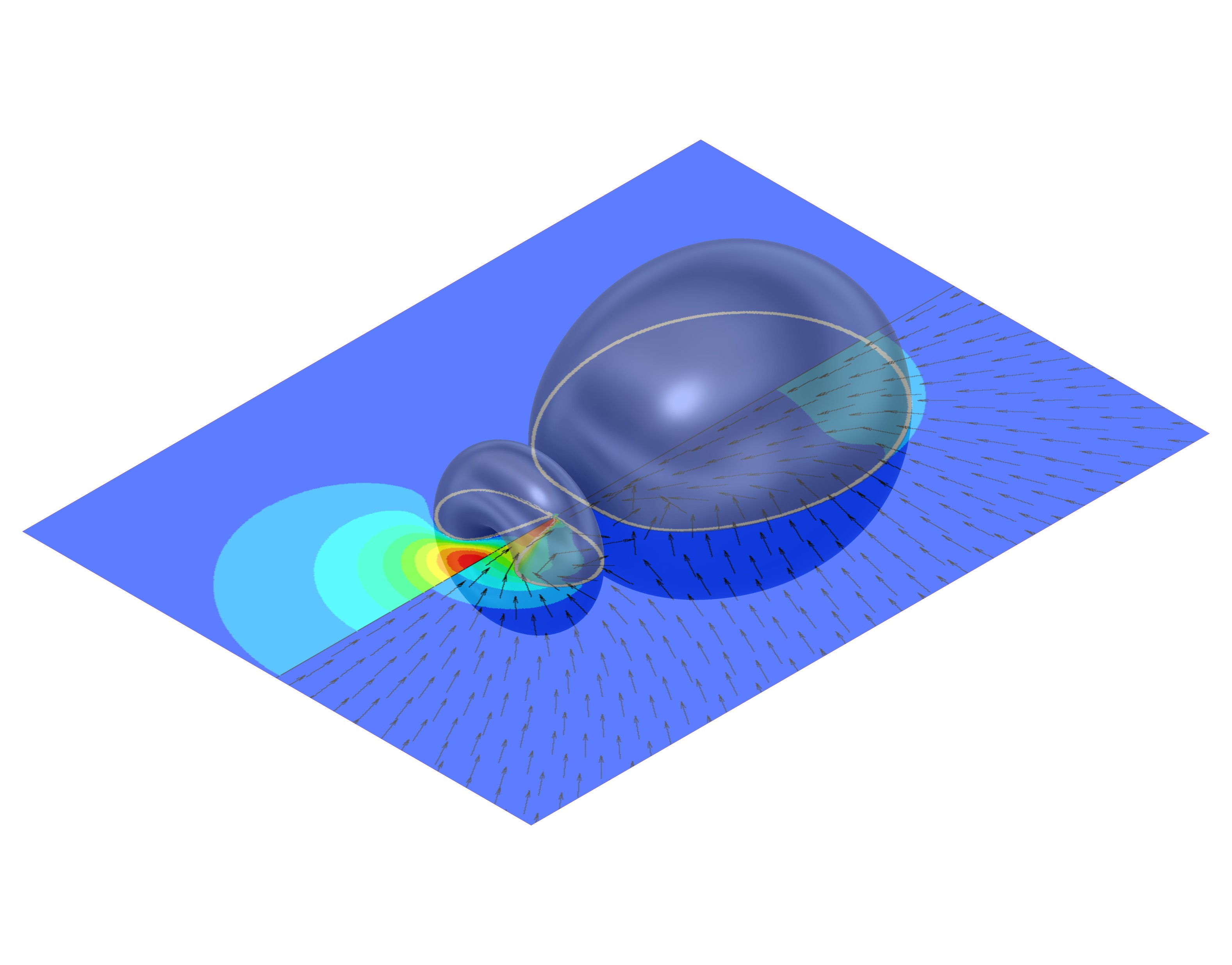
Soft Impact
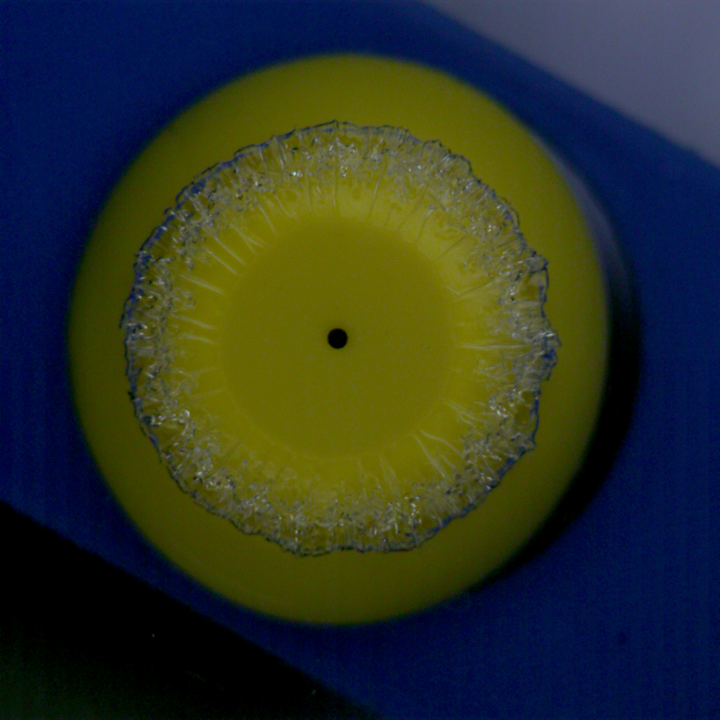
Impinging jet to perforated plates
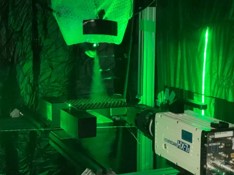
Thrust and transport Characteristics of Synthetic Jets
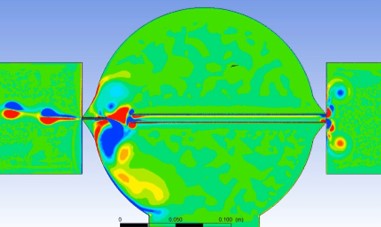
Urinary flow rate estimation using sparse singular value for portable urinary flow measurement devices
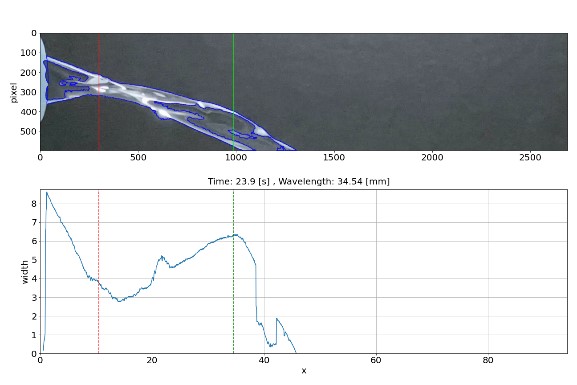